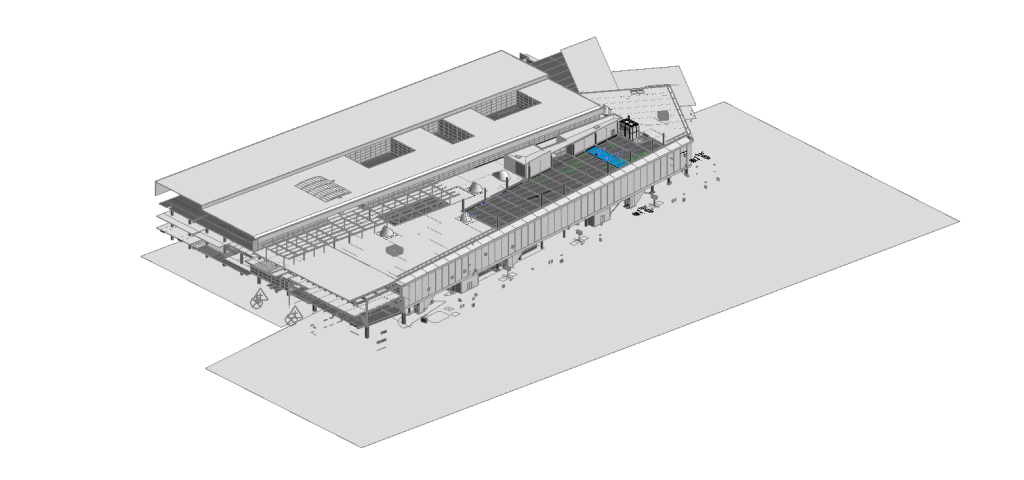
Schiphol Lounge 2
Project info:
Deerns was working on the renovation of Schiphol Airport. The main idea of the project was to provide new security equipment, that will reduce heat and power demand. In that process, we were specifically hired for Schiphol Lounge 2 area.
Client brief info:
Deerns is an independent engineering firm specializing in providing technical consulting and engineering solutions, with over 600 staff members around the globe. They have done successful projects for many Airports, Health Care organizations, Data Centers, Laboratory and Cleanroom users, and Commercial Real Estate developers. With their business operating since 1928, they are able to tailor their approach to every client's unique needs and specifications.
The Challenge:
To prepare an as-built model before DEERNS begins the design phase, we were asked to create a coordination model according to DD2 of the Schiphol datadrop delivery structure. The main task was to model all MEP disciplines according to the current As-Built Drawings delivered in Autocad Format.
Various disciplines and elements, like Rainwater, Wastewater, Heating, Cooling, and Fire Alarm Installations were to be modeled according to the delivered AutoCAD revision drawings. This made the task needed a great level of accuracy. Additionally, Schiphol had very specific data level requirements, which required additional coding expertise.
In addition, the complete model had to be delivered within 3 weeks so that the design team would not be delayed.
If we summarize it, this task challenged our processes, as well as the precision of our engineers.
The Approach:
In order to maintain our high standards at Deerns and Schiphol airports, a clear work breakdown structure of the spaces and disciplines in conjunction with a strict planning process and of course our "5 steps to BIM Dreamland" principle was again helpful.
The Outcome:
We successfully completed the task within three weeks and one review session. Once again, DIBS42 delivered on time and with exceptional quality, providing a coordination model ready for DEERNS' design phase. This simplified their process by eliminating the need to sift through countless DWG drawings, as we supplied a single, reliable source of information for as-built coordination. This approach not only saved time but also ensured greater efficiency and accuracy. The provided model has enabled the Deerns team to make any further design easier to coordinate and connect. It all led to a smoother execution of the design phase.
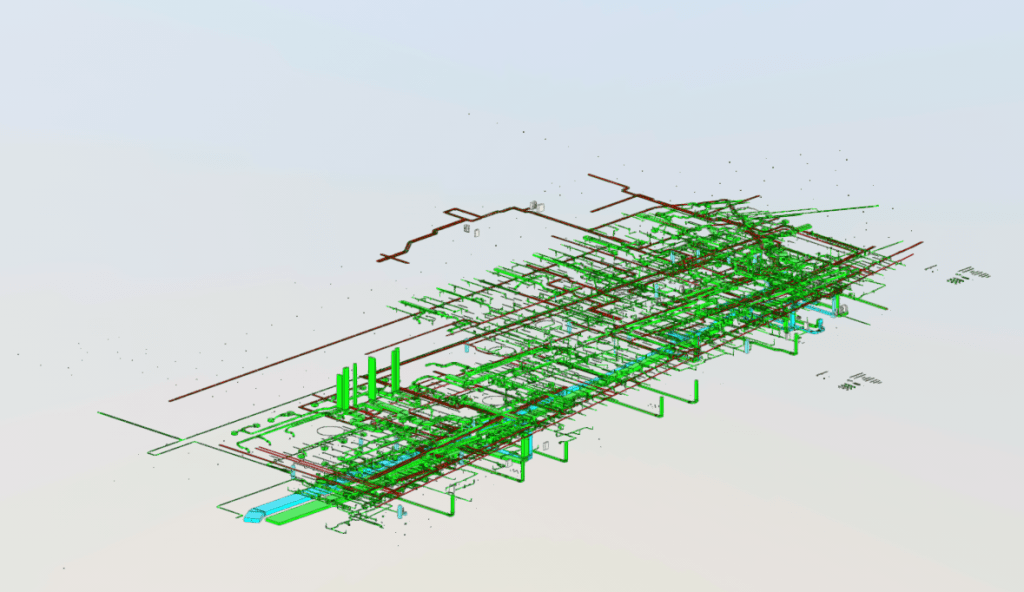
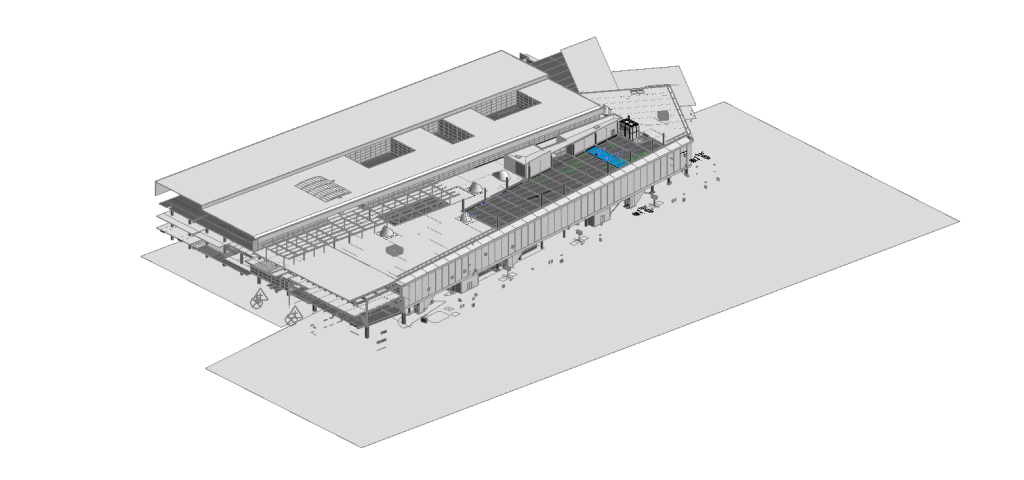