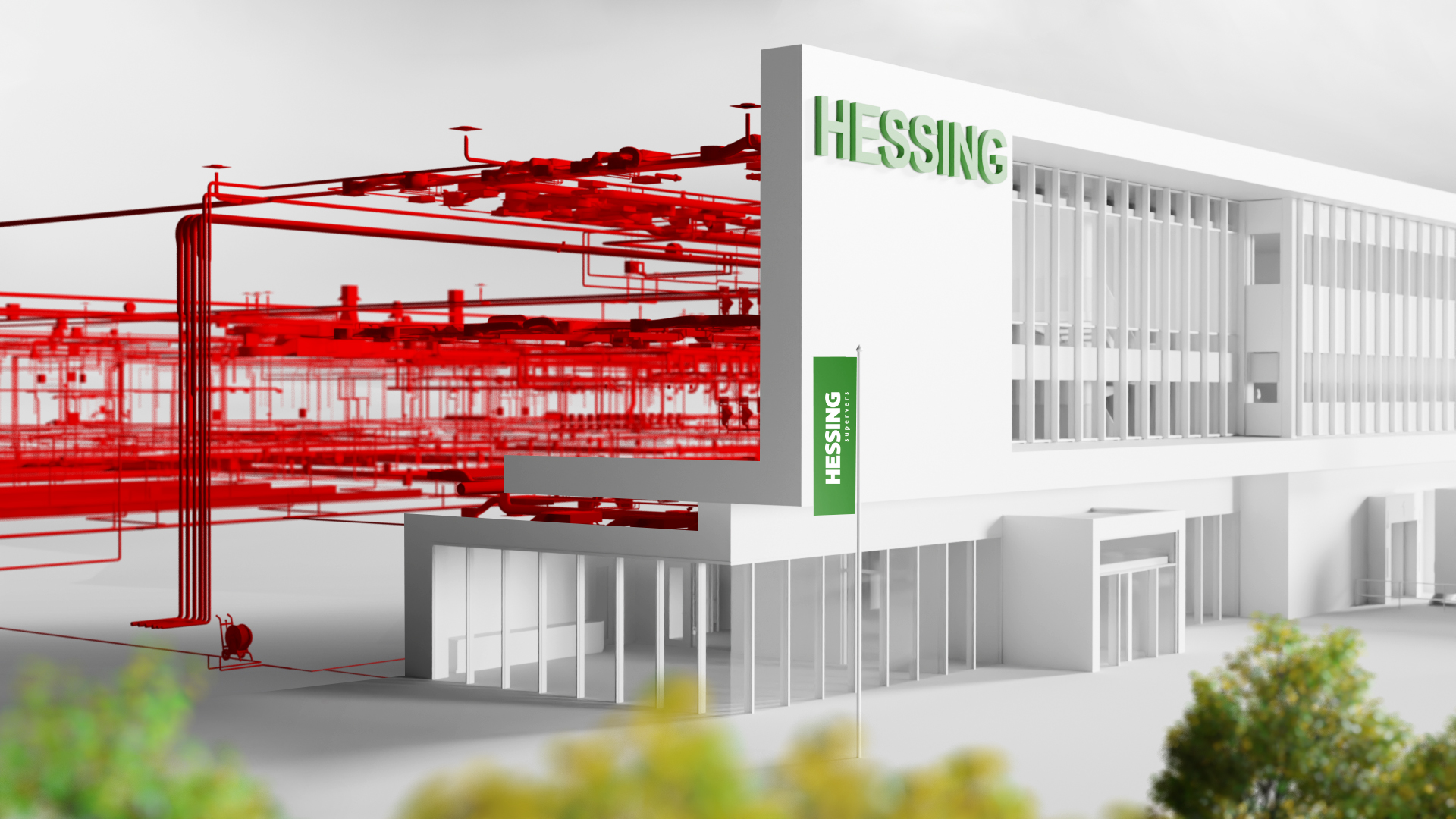
Hessing Supervers – done right in the first try!
Introduction
Hessing is proud to help hundreds of thousands of people every day in making healthy food choices. They produce ready-to-eat cut vegetables, fruit, fresh packs, and complete meal salads at five different locations. DIBS42 was involved in the construction of the latest production facility in Greenport Venlo and produced the BIM MEP model for it, done right in the first try! And we're proud of that!
New factory - sustainability first
Hessing Supervers' new factory was completed in 2023 and is built on a plot of over 100,000 m2, with the factory itself having a ground area of 45,800 m2 and two floors totaling 16,200 m2. The new production facility built in Greenport Venlo aims to meet the growing demand for cut vegetables. The facility is designed to process more than 320,000 kilos of raw materials daily on over a hundred production lines into 850 fresh products, working with the highest hygiene standards for the food industry. Hessing Supervers can call itself the most sustainable Fresh Vegetable Factory in Europe. Solar panels partly generate energy, and the energy and residual heat released during product cooling is reused for heating the offices.
BIM model and it’s disciplines
DIBS42's assignment on this project was to model all mechanical installations, excluding sprinkler and refrigeration technology, and to contribute to the detailed engineering. They were also responsible for the interdisciplinary coordination of these installations and ensuring that construction could be carried out as optimally and clash-free as possible based on the model.
From Technical Design to As-built in One Take
Djorhia Nijssen Treskes was the coordinating BIM Boss from DIBS42 during the realization.
"The engineering team had the task of starting with the first sketches from the preliminary design phase, after which, in close collaboration with the engineering department, the most effective solution was invented and developed. Our primary focus was on ensuring functionality, efficiency, and cost-effectiveness for both the design and modelling. By communicating daily with the execution team during the construction process, we were able to adjust the model in real-time according to the contract and reality. As a result, the model was made once from the pre-design phase, used during realization, and delivered to the final As-Built situation at completion, and we're naturally very proud of that!!" Djorhia enthusiastically claims.
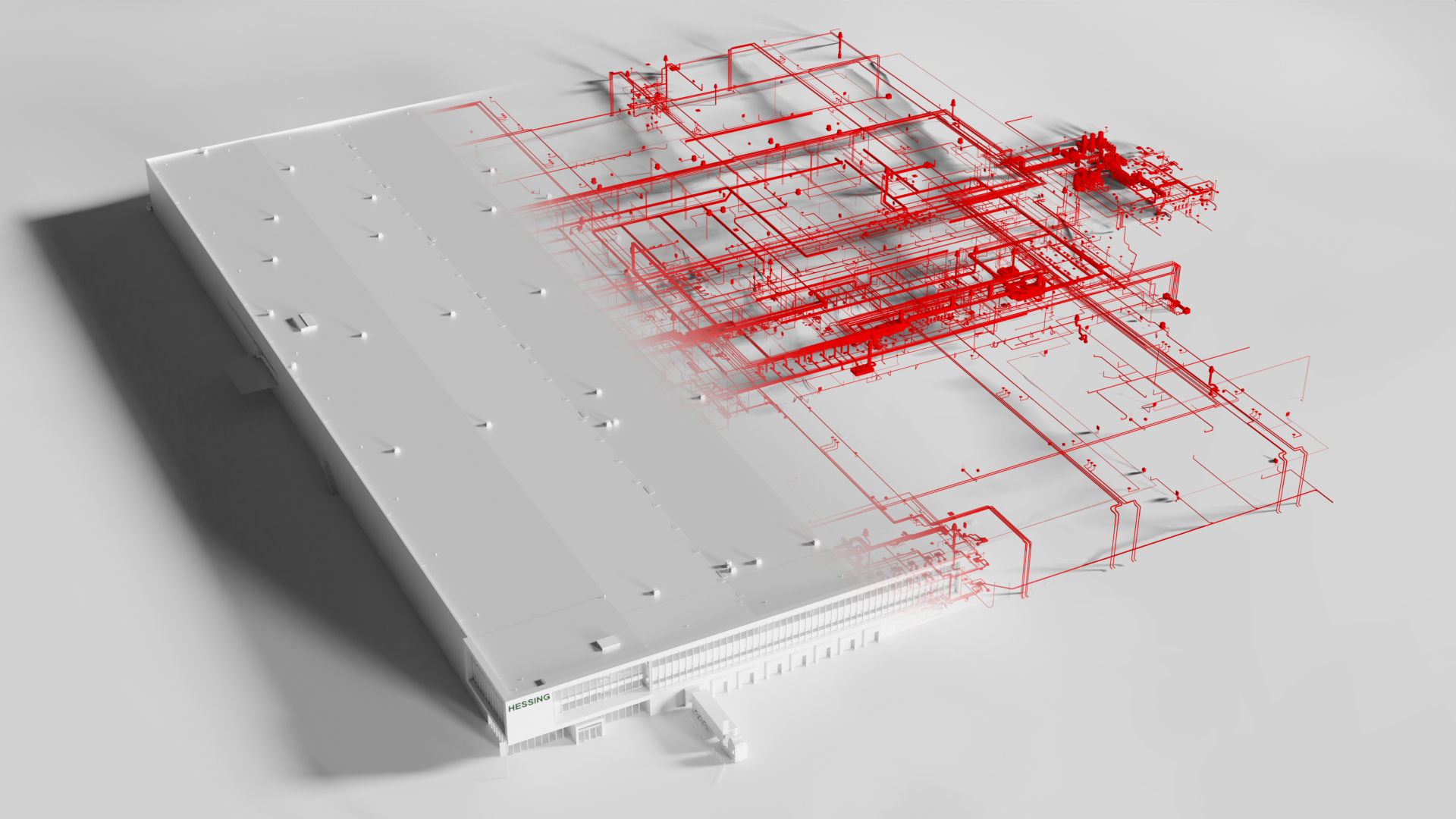
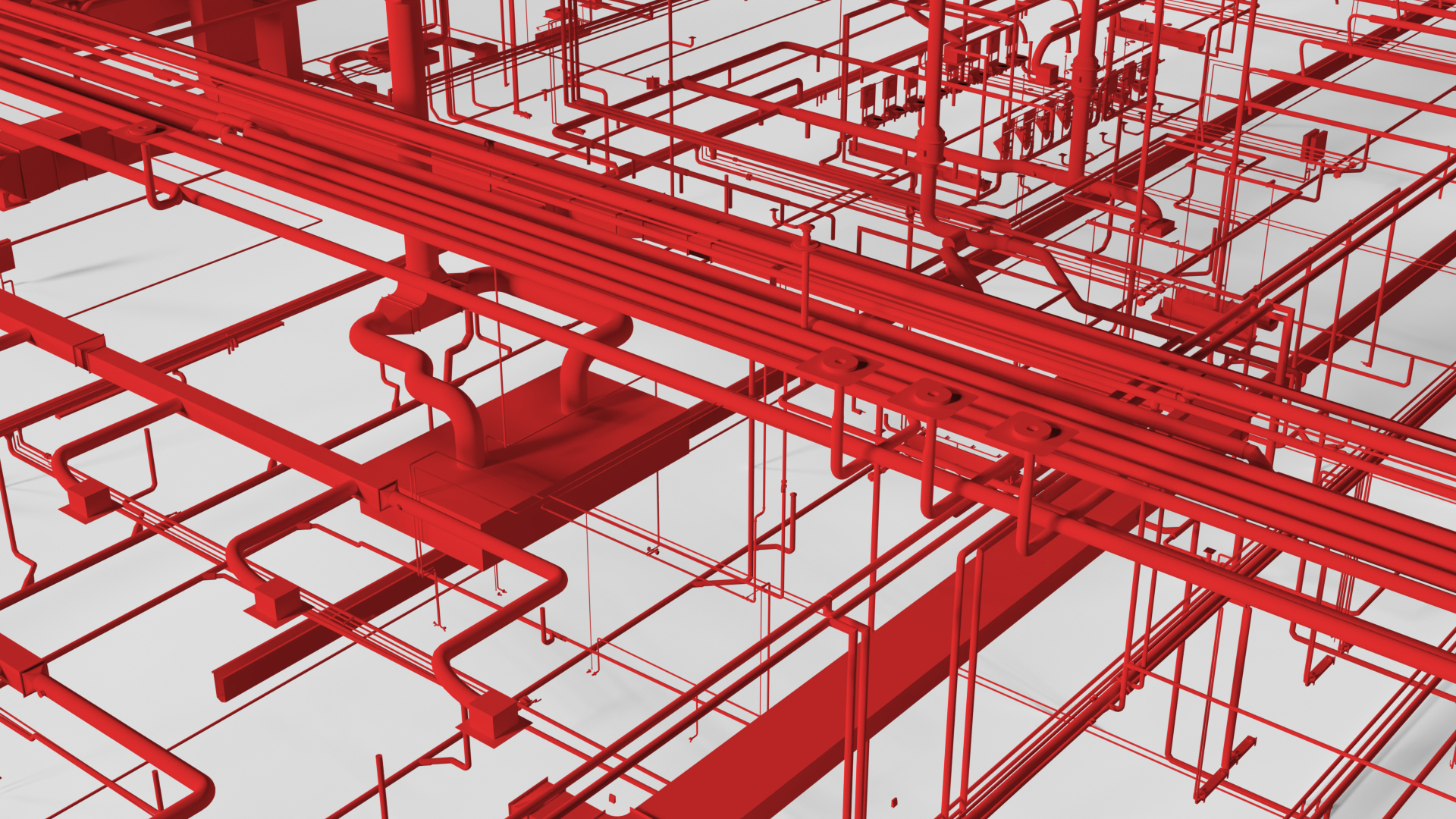
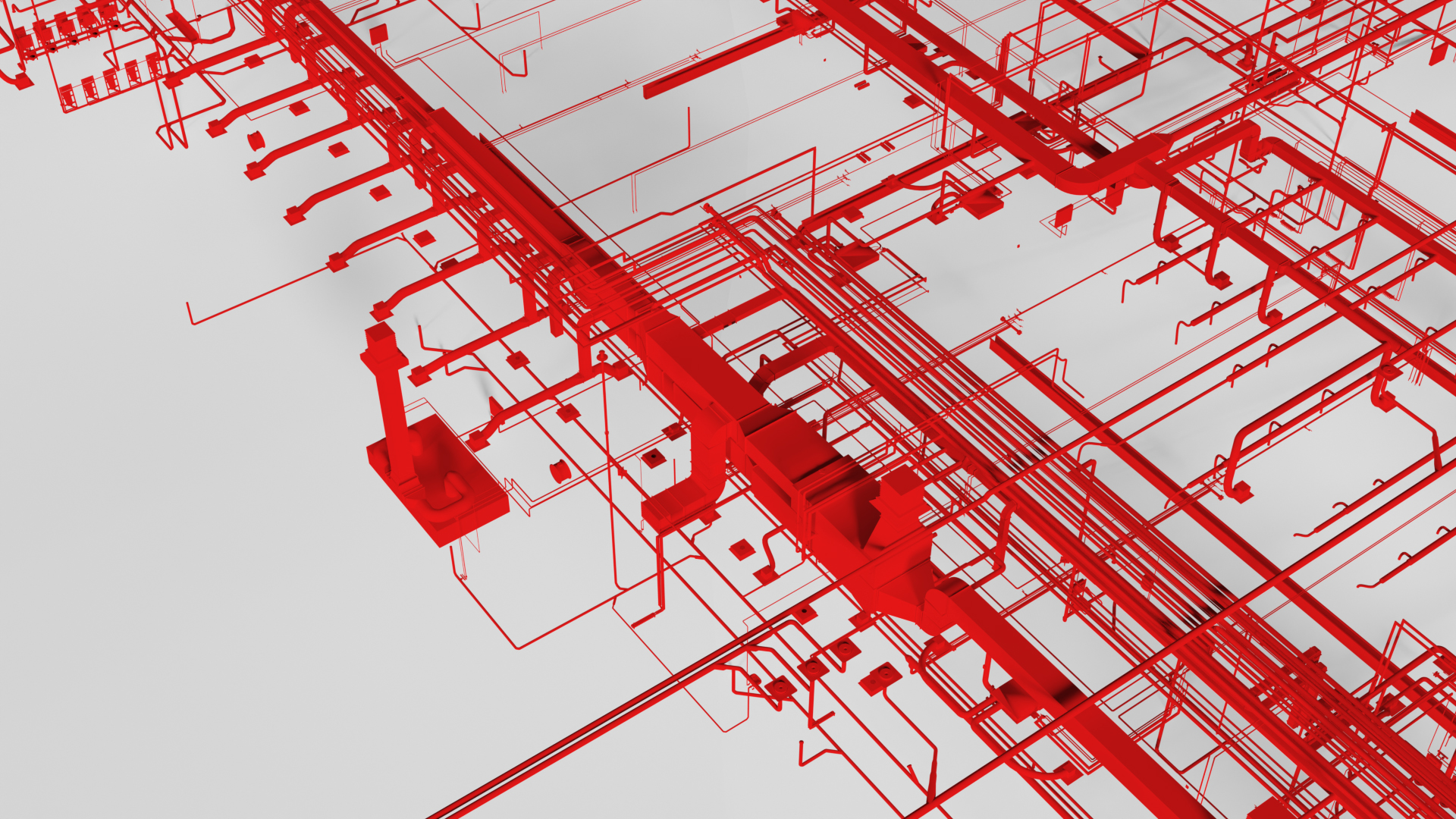