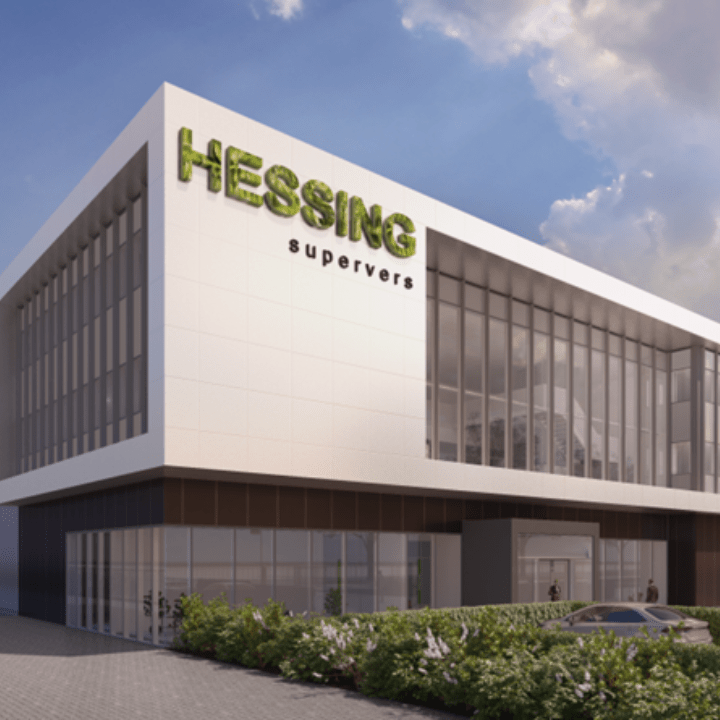
Green Future Hessing Venlo
Project info:
Hessing has constructed a new production facility in Greenport Venlo, with an aim to meet the growing demand for sliced vegetables. The facility was designed to process over 320.000 kilos of raw materials into 850 fresh products daily.
On a land parcel exceeding 100.000m2, the factory has a ground area of 45.800m2 and two upper floors totaling 16.200m2. Due to the purpose of the factory itself, it houses state-of-the-art equipment, and more important, complies with rigid sustainability, safety, and food hygiene standards.
Our role on the project was to create all virtual mechanical installations, besides cooling and sprinklers. We air handling systems, heating systems, water supply systems (hot and cold), sewage systems, rain water systems, ventilation systems. BIM Modeling, design, detail engineering.
As members of the engineering team, our task involved the modeling and design phase, referred to as "Voorontwerp" in Dutch, starting from the predesign stage. We initiated the process with preliminary sketches and collaborated closely with the engineering department to develop the most effective solution. Our primary focus was on ensuring functionality, efficiency, and cost-effectiveness in both the modeling and design aspects. The model itself served as the main source of information for our team, guiding us towards the creation of the best and most economical solution. Throughout the entire process, DIBS42 ensured that all aspects were modeled in accordance with the contract, following the optimal solution from the predesign phase to the final As-Built situation.
Client brief info:
Our work was done for vanPanhuis Installatietechniek, which are now a part of Hoppenbrouwers Techniek.
The Challenge:
The fundamental purpose of the building is that it is a (vegetable cutting) factory for food products, with that meaning it has a lot of diverse MEP installations. The technical ceiling is filled with meters and meters off complex MEP installation to make sure the factory works as optimal as possible.
Our communication skills were also put to the test, due to collaboration with different subcontractors.
The fluidity of the project was another challenging factor, with frequent design changes demanding rapid, effective responses.
Overall, this project has given us a chance to demonstrate our flexibility, experience, and our structured way of work.
The Approach:
Our flexible and adaptive approach, which is centered on the evolving needs of the project gave us a good starting point. At first, we took a broader perspective, which later we narrowed down specifically. All the time, our communication with the engineering team and site manager was maintained seamlessly. But what made the biggest impact was our highly optimized model and workflow that allowed us to quickly adapt to changes per the client’s demands.
The Outcome:
Our communication flow ended up eliminating the need for the complete revision phase. On-site people reacted quickly to the latest model changes, and therefore, in the event of anomalies on-site the model was updated swiftly, so those people could have the correct drawings within a four-hour window.
After construction was completed, the model was compared to the actual build, and a perfect match was revealed, enabling no revisions to be made to the construction drawings later on. (bold this no revision) a great achievement of the whole team!
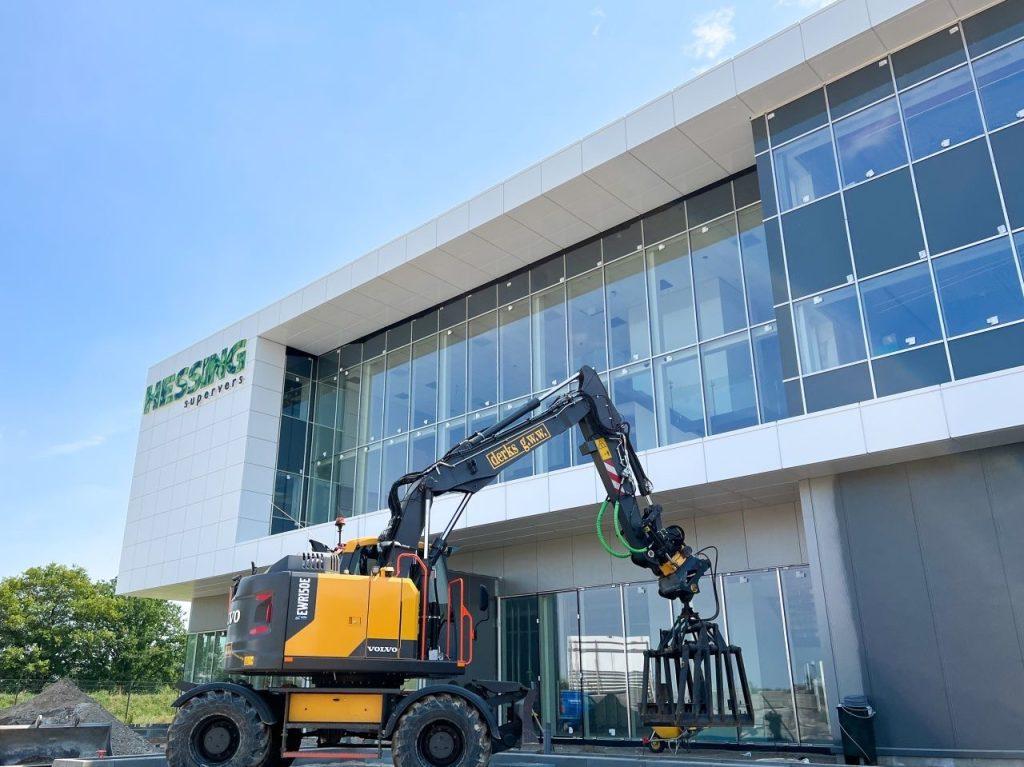
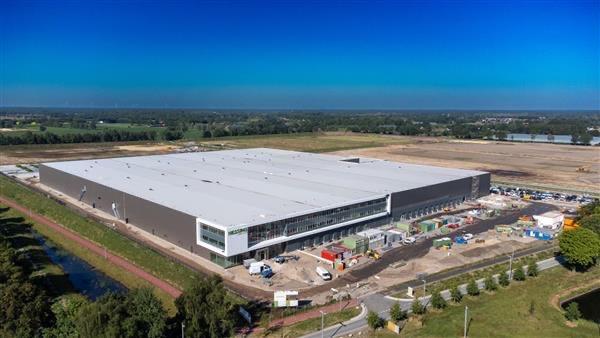