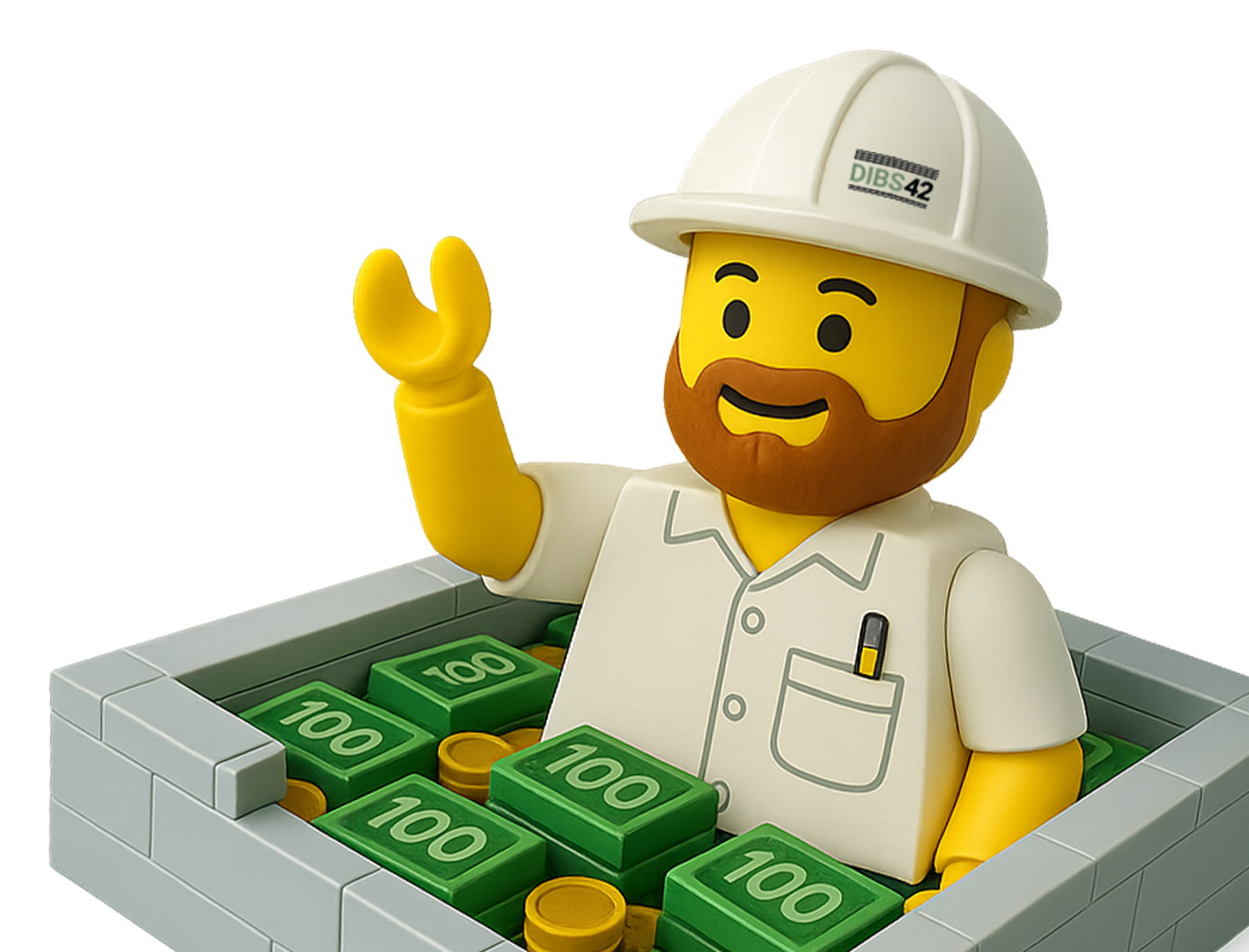
5 reasons why BIM models will save you money
The construction industry is evolving faster than ever. A study by McKinsey & Company shows that, on a global scale, the construction industry grows by 1% per year. With increasing labor and material costs and shorter project deadlines, companies are searching for solutions to stay competitive and ensure steady growth. One of the most effective strategies is implementing BIM models.
BIM (Building Information Modeling) is a smart way to plan and manage construction projects. Instead of traditional 2D blueprints, BIM uses digital 3D models of buildings that contain all necessary information – from dimensions and materials to costs and deadlines.
With BIM, all project stakeholders (architects, engineers, investors) can visualize how the building will look and function before construction even begins. This helps reduce errors, improve coordination, and lower costs. In short, BIM saves time, money, and enhances construction quality.
Given all these benefits, BIM implementation will undoubtedly increase project efficiency. With labor and material costs rising, we focused on cost savings and compiled five key reasons why BIM models will save you money.
1. Better maintenance and lower long-term costs
Buildings remain significant cost centers even after construction is completed. Studies indicate that 80% of a building's total costs occur during its lifespan – through maintenance, repairs, and renovations.
One of the major benefits of BIM implementation is that it allows building owners to have an exact digital record of all materials, systems, and components. When repairs or replacements are needed, all information is available in one place—eliminating the need for scanning, manual calculations, and unnecessary work. Of course, this is only possible if the construction process follows the model and all on-site changes are properly communicated back. In other words, a BIM building must be delivered with a validated as-built model to ensure these benefits are truly realized. In short, every MEP component’s exact location and details are stored in the BIM model, or, it can be linked through a Common Data Environment (CDE).
Result?
- Lower long-term maintenance costs
- More efficient facility management
- Increased property value
2. Smarter building: Integrated building solutions that save up to 30%
A McKinsey & Company study revealed that up to 30% of construction costs are spent on fixing errors, design modifications, and unforeseen issues. (McKinsey Global Institute, "Reinventing Construction: A Route to Higher Productivity", 2017)
One of the biggest sources of additional costs in construction is errors in design and coordination between all project participants.
BIM models do not only detect potential issues before construction begins but also enable fully integrated design. Through detailed simulations and clash detection tools, BIM will help prevent conflicts between MEP (mechanical, electrical, and plumbing) systems, architectural, and structural elements. More importantly, it supports a design process that prioritizes what’s best for the project as a whole—not just for individual disciplines. One common mistake is assigning separate budgets for each discipline, which often creates bottlenecks and hinders true integrated design and production.
Result?
- Fewer unforeseen costs
- Improved integration and coordination of MEP systems
- Simplified manufacturing processes
- Easier system maintenance
- Fewer breakdowns due to optimized routing and design
- Fewer project delays
- Better budget control in execution stage
3.Potential for more accurate planning and cost optimization
Traditional cost estimation methods are prone to errors, and discrepancies between initial estimates and actual costs are common. By using BIM models, which incorporate cost data, investors and contractors gain a clearer understanding of project expenses. Cost estimation becomes significantly more accurate when such models provide a transparent overview of material costs.
Studies suggest that BIM implementation reduces cost variations by up to 40% compared to traditional planning methods. (Dodge Data & Analytics, "The Business Value of BIM for Owners", 2014)
Result?
- More precise budgeting
- Lower risk of cost overruns
- Increased security for investors
4. More efficient and sustainable material management with less waste
According to the World Economic Forum, the construction industry generates over 30% of global waste. A significant portion of this waste comes from poor planning, over-purchasing, and lack of coordination.
BIM helps reduce this by enabling precise material tracking, better coordination across disciplines, and shifting more work to controlled production facilities. Off-site manufacturing not only minimizes the impact of unpredictable site conditions but also speeds up construction and significantly reduces material waste. Additionally, BIM improves logistics and storage planning, lowering warehousing and transportation costs.
Result?
- Less waste
- Lower material costs
- Reduced logistics and storage expenses
5. Faster and more efficient construction
Time is money, and this is especially true in the construction industry. Delays can increase project costs and threaten profitability.
BIM models help optimize the the manufacturing and construction stages by allowing contractors to precisely plan every step before work begins.
BIM models help optimize the manufacturing process and duration of construction stages by allowing contractors to precisely plan every step before work begins. Digital simulations of the construction process reveal which tasks can be performed simultaneously, reducing construction time by up to 20%. (McGraw-Hill Construction, "The Business Value of BIM", 2009)
Result?
- Shorter construction timelines
- Reduced labor costs during the construction phase
- Being able to build in shorter period of time
Conclusion
BIM is a proven and modern solution for reducing costs and increasing efficiency in the construction industry – across the entire lifecycle of a building. From enabling integrated design and reducing errors, to optimizing material use, speeding up construction, and lowering long-term costs. The benefits are clear and measurable.
If you haven’t implemented BIM in your projects yet, now is the time. Research mentioned before shows that construction companies and building owners who use BIM achieve up to 20% higher profitability compared to those who do not use this technology.
Smart construction starts with smart planning — and BIM is how we make it simple.
Do you also want to save money on projects? Contact DIBS42 and plan a video call with CEO and Founder Dennis Mulch.
Resources:
MGI-Reinventing-Construction-Executive-summary.pdf
McKinsey & Company - REINVENTING CONSTRUCTION: A ROUTE TO HIGHER PRODUCTIVITY FEBRUARY 2017
Business_Value_of_BIM_for_Owners_SMR_(2014).pdf
Dodge Data & Analytics, "The Business Value of BIM for Owners", 2014
Cost Analysis of Inadequate Interoperability in the U.S. Capital Facilities Industry
Cost Analysis of Inadequate Interoperability in the U.S. Capital Facilities Industry, U.S. Department of Commerce Technology Administration 2017